Lott company uses a job order – Embarking on the intricacies of Lott Company’s job order costing system, we unveil a world of meticulous cost management and informed decision-making. This narrative explores the nuances of this costing method, unraveling its benefits, challenges, and the profound impact it has had on Lott Company’s financial landscape.
Lott Company’s adoption of job order costing has been a transformative endeavor, empowering them with the ability to accurately track and assign costs to individual jobs, ensuring transparency and precision in their operations.
Job Order Costing System Overview
Job order costing is a method of accumulating and assigning costs to individual jobs or batches of production. It is typically used in industries or businesses where products are produced or services are provided on a custom basis, and the costs associated with each job or batch need to be tracked separately.
Key characteristics of a job order costing system include:
- Costs are accumulated for each individual job or batch.
- Job cost sheets are used to track the costs associated with each job.
- Costs are assigned to jobs based on actual usage or estimates.
- Overhead costs are applied to jobs based on a predetermined overhead rate.
Job order costing is commonly used in industries such as construction, manufacturing, and printing, where each job or batch is unique and requires its own set of materials, labor, and overhead costs.
Lott Company’s Job Order Costing System
Lott Company uses a job order costing system to accumulate and assign costs to individual jobs. This system is designed to track the costs associated with each job, from the initial estimate to the final completion. Lott Company’s job order costing system is based on the following principles:
Costs are accumulated for each job in a job cost sheet. Job cost sheets are used to track all of the costs associated with a particular job, including direct materials, direct labor, and manufacturing overhead.
Lott Company uses a job order costing system, which means that costs are accumulated for each individual job. This is in contrast to a process costing system, which is used when products are produced in a continuous flow. For example, a firefighter preparing for the firefighter 1 & 2 exam prep would use a job order costing system to track the costs of their preparation, such as the cost of study materials and the cost of taking the exam.
This information would then be used to determine the total cost of the preparation.
Costs are assigned to jobs based on the actual costs incurred. Lott Company uses a variety of methods to assign costs to jobs, including actual costing, normal costing, and standard costing.
The job order costing system provides Lott Company with the information it needs to track the profitability of each job. This information is used to make decisions about pricing, production, and marketing.
Cost Pools and Cost Drivers, Lott company uses a job order
Lott Company uses a variety of cost pools and cost drivers in its job order costing system. Cost pools are groups of costs that are assigned to jobs based on a common cost driver. Cost drivers are factors that cause costs to vary from job to job.
Some of the cost pools and cost drivers used by Lott Company include:
- Direct materials cost pool: The direct materials cost pool includes the cost of all materials that are used directly in the production of a job. The cost driver for the direct materials cost pool is the quantity of materials used.
- Direct labor cost pool: The direct labor cost pool includes the cost of all labor that is used directly in the production of a job. The cost driver for the direct labor cost pool is the number of hours worked.
- Manufacturing overhead cost pool: The manufacturing overhead cost pool includes the cost of all indirect costs that are incurred in the production of a job. The cost driver for the manufacturing overhead cost pool is the machine hours used.
Benefits and Challenges of Using a Job Order Costing System
Implementing a job order costing system offers several advantages to Lott Company. This system provides detailed information on the costs incurred for each job, enabling accurate pricing and effective cost control. Furthermore, it facilitates timely decision-making by providing up-to-date data on job profitability.
However, certain challenges arise when using a job order costing system. Accurately allocating indirect costs to specific jobs can be complex, leading to potential inaccuracies in cost calculations. Additionally, the system requires a significant amount of data collection and processing, which can be time-consuming and resource-intensive.
Overcoming Challenges
To overcome these challenges, Lott Company should consider the following recommendations:
- Establish clear and consistent guidelines for allocating indirect costs to jobs.
- Invest in software or technology to automate data collection and processing.
- Regularly review and refine the job order costing system to ensure accuracy and efficiency.
Financial Reporting Implications
Job order costing significantly impacts Lott Company’s financial statements, particularly the income statement and balance sheet. It affects specific line items, including cost of goods sold, inventory, and work in process.
Under job order costing, the cost of goods sold is determined by the actual costs incurred in producing each job. This provides a more accurate representation of the cost of products sold compared to other costing methods, such as process costing, which assigns costs based on estimated averages.
Balance Sheet
Job order costing also affects the balance sheet. Work in process inventory represents the costs of jobs that are still in production. This account is updated as costs are incurred and jobs are completed, providing a more accurate picture of the company’s inventory valuation.
Case Study or Example: Lott Company Uses A Job Order
Lott Company, a manufacturer of custom furniture, has successfully utilized its job order costing system to make informed business decisions that have significantly impacted its efficiency, profitability, and customer satisfaction.
Improved Efficiency
By tracking costs associated with each job, Lott Company can identify areas where inefficiencies occur. For instance, they discovered that a particular production process was taking longer than necessary due to inadequate equipment. The company invested in upgrading the equipment, resulting in a substantial reduction in production time and associated costs.
Increased Profitability
Job order costing provides accurate information on the profitability of each job. This data enables Lott Company to adjust its pricing strategy to ensure adequate profit margins. Additionally, by identifying unprofitable jobs early on, the company can take corrective actions to minimize losses.
Enhanced Customer Satisfaction
Accurate cost information allows Lott Company to provide competitive quotes to customers. Moreover, by understanding the costs associated with each job, the company can effectively manage customer expectations and ensure timely delivery of high-quality products.
Lessons Learned and Best Practices
Lott Company’s experience with job order costing has highlighted several valuable lessons and best practices that can benefit other companies:
- Accurate Data Collection:Accurate cost data is crucial for effective decision-making. Lott Company emphasizes the importance of meticulous record-keeping and regular audits to ensure data integrity.
- Regular Cost Analysis:The company conducts regular cost analyses to identify trends and potential areas for improvement. This ongoing evaluation enables proactive adjustments to processes and strategies.
- Employee Involvement:Lott Company involves employees in the cost-saving process by providing training and incentives for identifying and implementing cost-effective measures.
Answers to Common Questions
What are the key advantages of using a job order costing system?
Job order costing provides accurate cost tracking for individual jobs, enabling better decision-making, improved profitability, and enhanced customer satisfaction.
What challenges might Lott Company face in implementing a job order costing system?
Lott Company may encounter challenges in data collection, cost estimation, and ensuring accuracy throughout the costing process.
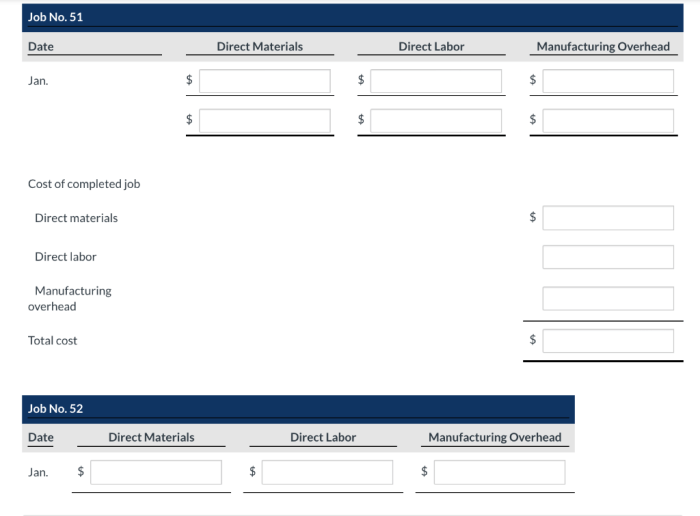